催化裂化装置节能降耗的有效途径论文
“海盐Kong”通过精心收集,向本站投稿了13篇催化裂化装置节能降耗的有效途径论文,下面是小编为大家整理后的催化裂化装置节能降耗的有效途径论文,仅供参考,欢迎大家阅读,希望可以帮助到有需要的朋友。
篇1:催化裂化装置节能降耗的有效途径论文
1.1降低催化裂化反应中的焦炭产率
根据我国现有的炼油生产工艺分析,焦炭是催化裂化装置中反应所占能耗最大的部分。焦炭主要类型包括催化焦、污染焦、附加焦等,呈现出多种混合状态。具体的措施如下:第一,使用焦炭产率较低的催化剂产品。催化剂虽然不直接进行催化裂化反应,但其本身作用于装置中依然消耗能源,采用焦炭产率较低的催化剂是最简单、最实用的方式,而且催化裂化装置也不需要额外的添加辅助设备,不需要进行改造。第二,使用焦炭产率较低的工艺设备。除了催化剂本身的焦炭产率特性之外,还可以通过工艺设备的合理应用来实现降低目的。催化裂化装置中的主要组成部分包括原料喷嘴、气提段、提升管出口快分等,一些新的工艺设备主要通过改变原来的反应状态实现,如将液态转化为气态;总体而言,工艺设备的选择标准时改善原料,减少工艺气与催化剂的接触,增强气提效果等。第三,使用焦炭产率较低的原材料。石油中的沥青、胶质、石蜡和重金属成分等是影响焦炭产率的主要原因,针对催化裂化的原材料而言,需要进行事先预处理。目前,在节能减排、低碳观念的影响下,我国对石油原材料预处理的手段主要包括循环技术和冷却技术,以提高反应剂的效率,降低碳差;同时,对原材料进行预处理可以有效提高轻质油产量。
1.2降低催化裂化反应中的综合电耗
催化裂化装置工作中要消耗大量的电能,约占整个工艺流程装置总电能消耗的10%,对炼制企业而言是一笔巨大的经济投入。降低电能消耗不仅可以节约成本,同时也做到了低碳排放。首先,优化烟机运行,提高回收功率。烟机即烟气轮机,是催化裂化装置中发挥能量回收的设备,其运行的优劣对电能损耗的影响十分明显。可以适当降低主风机出口到烟机入口的压力,减小运行负荷,定期清理结垢和粉尘,确保烟气轮机的平稳、长期、高效运转。其次,完善空冷器和机泵的节电措施。与烟机相比,空冷器和机泵的电力消耗较小,设备的功率有限,但由于工艺限制,这两种设备在整个工艺流程中数量较多,整体电能消耗综合起来也是相对庞大的,因此有必要进行节能措施改造。根据不同类型的空冷器和机泵设备,采用合适的级恩恩个手段,如对于流量或负荷调节频繁的机泵而言,可以改装为变频装置控制的体系。再次,增加蒸汽产量并降低蒸汽消耗。石油炼制工艺中需要用到大功率热工设备,控制不当的情况下会导致催化裂化装置中热量剩余过多,造成浪费;蒸汽量过多,反应装置内的'压力就会增加,但重质油在催化裂化装置中反应所需要的压力级别是固定的(3.5MPa),过多的蒸汽只会造成无效损失。因此,可以减少单位时间内的蒸汽供给,适当延长炼制时长,实现低压生产的目的。除此之外,还可以采取提高富气压缩机入口压力的方式,优化余热锅炉运行等方式展开催化裂化工艺生产;目前,中石化公司对加强装置间热联合的生产工艺进行了大规模改造,并开发了一系列具有自主知识产权的催化裂化装置,这对我国石油炼制行业催化裂化装置节能降耗有重要的借鉴价值。
2结语
石油资源的巨大需求量带动了石化产业的快速发展,市场竞争也日渐激烈,炼油企业要在市场上赢得一席之地,必须在资源限制条件下进行技术改造,降低生产成本,提高生产效率,同时按照国家相关规定满足环境保护的要求;催化裂化装置作为炼油生产中的关键设备,在整个工艺流程中能耗所占的比例较大,除了要针对装置进行优化改造之外,还要考虑到原料性质、催化剂属性、配套装置等应用。总地来说,提高催化裂化装置的节能降耗能力,对我国的石油炼制产业具有巨大的推动作用。
篇2:MTBE装置节能降耗探讨论文
MTBE装置节能降耗探讨论文
摘要:MTBE作为最常用的化学试剂和反应溶剂在化工产业中的应用非常广泛。由于MTBE能够对环境产生污染,所以必须要加强MTBE装置的节能降耗处理。本文通过对于MTBE装置节能降耗进行分析,明确其节能降耗的主要措施,从而增强化工产业绿色发展的水平。
关键词:MTBE装置;节能降耗技术;存储管理
1、MTBE概述
工业甲基叔丁基醚(MTBE)主要以炼油液化气混合碳四和工业甲醇为原料,由于液化气碳四中的硫化物绝大部分富集到了MTBE中,因此,以炼油混合碳四为原料生产的MTBE的硫含量较高,一般低的在100μg/g左右,高的可达-3000μg/g。随着经济不断发展和对环保要求的不断加强,车用汽油的硫含量指标越来越严。目前在北京、上海、广州等经济发达的城市,车用汽油己执行硫含量小于10μg/g的国V排放标准,天津、河北、山东、长三角、珠三角实施汽油国V排放标准的时间也己提前。MTBE作为清洁汽油的调和组分,加入量一般在10-20%之间,因此将MTBE的硫含量降低到1Oμg/g以下,也是汽油质量升级到国V排放标准的必然要求。如果MTBE用作化工原料,则硫含量一般要求低于5μg/gMTBE中硫化物主要来源于生产原料混合碳四。在MTBE的生产过程中,MTBE比碳四烃对硫化物有更高的溶解性,且绝大部分硫化物的沸点较碳四烃的沸点高,因此,进料碳四中的硫化物绝大部分被富集到MTBE产品中。MTBE降硫有两个方向:一是降低原料的硫含量(即前脱硫工艺);二是对高硫MTBE进行脱硫处理(即后脱硫工艺)。河北精致科技有限公司,为适应国IV汽油质量升级开发了液化气深度脱硫技术(专利ZL10250279.8)。采用该项技术,一般催化液化气的总硫可降低到5μg以下,焦化液化气的总硫可降低到50μg/g以下。与该技术配套生产的MTBE产品总硫,可降低到了50μg/g以下,最低达到20μg/g。但针对国V汽油质量升级,目前国内使用的MTBE前脱硫工艺,存在着投资大、运行费用高、产品质量不稳定等缺点,为此,河北精致科技有限公司又开发了“一种低含硫甲基叔丁基醚的生产方法”专利技术。该技术工艺简单,对原料MTBE硫含量的适应范围宽(20-1200μg/g),产品质量稳定(硫含量控制在10μg/g或5μg/g以下均可),投资少,运行费用抵,无三废排放。配合液化气深度脱硫技术使用,还可大幅降低从液化气脱硫醇到MTBE后脱硫工艺过程的脱硫能耗,进一步降低低硫MTBE的生产成本。液化气经过脱硫醇后,液化气中的硫醇硫等活性硫化物,可以被彻底脱除,转化成高沸点的二硫化物,大部分被反抽提油带走,少量的留在液化气当中。经气分和MTBE生产过程后,由于MTBE比醚后碳四对硫化物有更高的溶解性,液化气中这些高沸点硫化物全部富集到了产品MTBE当中。根据沸点差,含硫MTBE经过蒸馏将高沸点硫化物从MTBE当中切除,是MTBE萃取蒸馏降总硫专利技术(专利公告号:10397611.0)的基本原理。对MTBE实施萃取再蒸馏,低硫的MTBE从塔顶蒸出,高硫馏分在塔底循环,高度富集了含硫化合物的副产物部分从塔底抽出,可作为加氢装置的原料。为了提高脱硫效果,降低MTBE损失,防止塔底发生生成胶质、缩聚、结焦反应,加入萃取防胶剂,优化工艺技术,是MTBE萃取再蒸馏技术有效手段。采用本项专利技术可生产硫含量10μg/g的MTBE产品,产品收率达到99%以上。适当降低收率时,硫含量可小于5μg/g。既可满足国V清洁汽油的调合,也可以满足作为化工原料的要求。
2、MTBE装置存在的主要问题
2.1甲醇回收系统腐蚀
由于MTBE装置在长时间使用之后设备会出现腐蚀的问题,其中甲醇回收系统的萃取塔受到腐蚀影响非常严重。通常情况下,如果萃取塔被腐蚀之后必须要针对萃取塔进行清理。在清理的过程中发现有鳞片状的黑色堵塞物和红褐色的锈蚀物,并且塔内的筛孔会被黑褐色的碎渣进行堵塞。通过对于这些物质进行磁性分析,能够进一步判断这些物质属于四氧化三铁。
2.2MTBE装置蒸汽用量存在问题
MTBE装置中通过异丁烯进行转化,是放热反应,生产的热量能够有效实现降低能耗。由于MTBE装置运行阶,段蒸汽消耗存在于甲醇回收塔以及催化蒸馏塔之间,所以催化蒸馏塔对低压蒸汽进行消耗。通过对蒸馏塔进行数据分析可以将不同的进料温度和塔底的'重沸器进行联系,通过灵敏板温度串级控制催化蒸馏塔蒸汽的流量,能有效的减少蒸汽量的使用量。
3、节能降耗的对策
3.1腐蚀问题的解决对策
首先如果MTBE装置的萃取塔发生腐蚀问题,是必须要加强对净化器的净化功能。通过进行有效过滤能够将甲醇的金属离子和碱性物质含量降低。同时要将甲醇萃取水的酸碱值进行重点监控,并且要定期检查萃取水的酸碱值。如果发现萃取水酸碱值过高,则必须要对甲醇回收系统进行定期换水,必要的情况下可以加入碱来中和控制萃取水的酸值,但是避免加入的碱过量。在MTBE装置开工之前,首先要加强磺酸基的控制与处理,所以必须要严格控制原料的预热温度,降低离子过滤器的反应温度。要严格控制醇烯比,通过有效控制甲醇醚化反应生成的水。可以避免因为弱水浸泡而出现酸基团脱落的现象。对于MTBE装置甲醇回收系统会受到吸氧腐蚀的影响,所以必须要通过在甲醇回收装置中安装除氧设备,保证设备的安全运转,同时也可以降低进料的温度。避免氧活性的提升,减轻管线腐蚀程度。
3.2提升进料温度
通过采取逆流的方式进行换热,在冷热物料温度不变的情况下,加强对于冷物料的出口温度管理,首先利用翅片式的换热器来扩大散热面积,促进流体的湍流保证散热效率的提升,其次,可以将传热表面制作成为凹凸不平的形状实现增加扰动的效果,降低边界厚度来加强热传导的效率。还可以利用小金属颗粒涂抹在传热表面,从而有效提升传热面积也能够增加散热器的效率,利用流体扰动,对不同的异型管安装螺旋圈或金属卷片,提高流体扰动速度。减少对于热阻的传导影响。在蒸馏塔进料量与催化蒸馏塔底液位设置串级控制系统;塔顶压力用间接调节冷凝器冷却面积的方式控制;为保证回流罐顶不形成负压,采用热旁路的方式进行控制;为防止紧急情况下,热旁路调节不能解决回流罐顶负压的问题时,可用手操器控制,以在回流罐顶补入氮气的方式解决;塔顶回流采用了流量和塔顶温度串级调节的方式控制;产品外送采用了流量和塔顶回流罐液位串级调节的方式控制;塔底温度采用了温度一流量串级调节。
4、MTBE的存储管理
由于MTBE属于无色液体,但是具有醚样气味,所以具有易燃的特点,尤其是其蒸汽能够与空气形成爆炸混合物,通常情况下。MTBE能够挥发成蒸汽,其蒸汽能对眼睛黏膜及上呼吸道产生强烈刺激,所以必须要加强,对于MTBE的包装有效管理,避免对环境造成污染。如果发生MTBE物质泄漏的问题,应该迅速撤离,泄漏污染区的人员至安全区,并且进行隔离,严格限制人员出入,切断火源,避免发生爆炸事故,对应急处理人员应该佩戴正压式呼吸器,并且穿戴消防服,尽可能快速的切断泄漏源,防止MTBE进入到下水道和排水沟等空间。如果发生小量的泄漏,可以采用沙土等其它惰性材料吸收,如果发生大规模的泄漏事故,则应该通过构筑围堤或者挖坑的方式,对泄漏出的MTBE进行回收。利用泡沫覆盖的方法,可以避免MTBE产生蒸汽与空气发生结合,防止引发爆炸事故。对于现场的操作,应该加强通风,并且对相关人员进行专门培训,严格提高专业技术,通过将操作参数控制在正常范围,对温度、流量和压力等参数曲线自动调节。同时不允许超出工艺设置的参数,保障设备与人员安全。设备全部采用露天布置,以利通风、散热。按有关规定设计消防系统,保证出现事故时,能进行有效的消防。依托现有装置进行职业卫生设计,达到安全卫生的要求。压力设备需设置安全阀。装置需设有可燃气体报警仪。储存、处理和输送易燃、易爆、物料的设备、管道需采取静电接地和防雷措施。
5、结语
本文通过对于MTBE装置的甲醇回收系统设备腐蚀以及蒸汽用量的影响入手,通过针对性的措施,来降低MTBE装置中催化蒸馏的进料温度,可以有效的节省蒸汽用量提高节能降耗的效果,但需要注意的是,在此过程中,不应该过度提高进料温度,因为很多没有转换的异丁烯在蒸馏塔中,会发生放热反应,并且会导致MTBE产品的二聚物含量增加。
参考文献:
[1]王照,孔祥军,李煜童.泄漏检测与修复技术在MTBE装置的应用研究[J].环境研究与监测,,30(02):60-62.
[2]计洪旭,纪燕飞.迷宫压缩机在MTBE装置热泵系统中的工业应用研究[J].压缩机技术,2017(01):34-36.
[3]刘初春.气体分馏、MTBE、烷基化装置组合优化,提高碳四资源利用水平[J].当代石油石化,,24(12):15-20.
[4]李红军.锦西石化MTBE装置应用脱酸剂改善萃取水水质降低设备腐蚀[J].化工管理,2016(11):6+8.
篇3:MTBE装置节能降耗解析论文
摘要:近年来,随着中国经济的不断发展,我们的化工事业也更上一层楼。MTBE作为一种常用的化学试剂和反应溶剂,在工业中的应用十分的广泛。但是MTBE作为一种具有毒性的,对环境有一定污染的化学品,它的使用我们应该及其注意。关于MTBE装置的节能降耗也迫在眉睫。本文就主要分析了MTBE的发展历程,主要用途,以及节能降耗的主要措施。
关键词:MTBE装置;节能降耗
MTBE是甲基叔丁基醚的英文简称,微溶于水,储存方便。它的使用在世界范围内已经十分广泛了,被应用于各个方面。随着各国对环保问题的重视日益加重,相继出台了对于含铅汽油使用限制的法律法规,这就为MTBE的迅速发展奠定了坚实的市场基础。
1MTBE的发展历程
自从各项关于含铅化学品使用限制的法规相继出台以后,MTBE就作为四乙基铅的替代品使用,从而大大提高了市场占有率,促进了其快速发展。MTBE真正开始被人们所关注是在20世纪70年代,作为提高汽油性能的调和剂而被人们所认识。1973年,意大利开发出了世界上第一套MTBE装置,投产后,每年可达到十万吨的产量,引起了各界的广泛关注,产量更是快速增长。而一直到1979年,我国才开始研究MTBE合成工业。相关研究一直持续到1983年,我国终于拥有了自己的化工型MTBE装置,建成后的增长速度也很快,产业规模迅速扩大。逐渐的,有了上海燕山、吉化、浙江信汇、抚顺等MTBE装置的相继投产。第一套采用催化蒸馏新工艺的年产四万吨的MTBE工业装置建成投产,标志着我国生产工艺水平进入到80年代先进水平。
2MTBE的主要应用
2.1汽油添加剂
因为MTBE能够与汽油完美的融合,具有很好的防爆性和稳定性,加之它与其他化学物相比不易氧化,因此经常被作为汽油添加剂来使用。添加了MTBE的汽油不仅仅拥有更强大的防爆性能和稳定性能,在一定程度上,他也是可以改变汽车的性能的,减少污染。简单分析来说,就是将MTBE与汽油融合后,能够增加汽油中的氧气含量,就可以降低尾气中的一氧化碳含量,能够降低汽车的尾气排放的污染量。
2.2化工用途
MTBE还可用于生产丁基橡胶、MMA等其他类型的化工品。最主要的.方面就是利用MTBE裂解高纯度的异丁烯并应用于精细化学品上面。除此之外,还有另外的主要的化工用途,就是丁基橡胶方面。一般的操作流程是国内购进MTBE,用于生产丁基橡胶的企业,例如燕山石化、浙江信汇等。而丁基橡胶近年来是主要被应用于内胎和轮胎的气密层,或者是用于制作医用胶囊。而近年来,中国经济增长带动了汽车需求量的增加,在带动丁基橡胶的同时也带动了MTBE的发展。
2.3医药用途
总的来说,MTBE的医药用途规模不大,因为作为医药中间体的MTBE的纯度要求、产品性状稳定性要求都很高,在国内,也仅仅只有几家企业的生产可以达到要求,这也是阻碍了MTBE在医药方面发展的主要原因之一。
篇4:MTBE装置节能降耗解析论文
3.1优化操作异丁烷塔
MTBE装置最重要的一个步骤就是异丁烷塔操作。异丁烷塔塔顶的异丁烷质量达到了百分之95以上,塔底的甲乙酮装置原料重碳四中质量小于百分之五。降低塔的回流量以后,就能降低塔的负荷。并且与原操作相比,每小时还可以节汽两吨。
3.2催化蒸馏塔顶冷却器与原冷却器并联使用
这种使用方法,可以有效降低回流量,达到降低压力的效果。在原来的生产方式下,塔顶只有一台催化蒸馏冷却器,那么当设备检修维护时蒸馏塔就会被迫携带着原料停工,闭路运行时的能耗消耗是极高的,优化操作后,就可以有效降低催化剂的床层温度优化运行条件,从而达到节能降耗的效果。
3.3塔底热源采用低温热水
一般来说MTBE装置的异丁烷塔重沸器,热源部分采用的水位大约在80至96度之间,夏季以异丁烷塔新增重沸器为主为主,冬季以原蒸汽热源为主,二者相互协调匹配和,通过调整蒸汽流浪控制塔底温度,能够依照具体情况而定灵活调整。可以每小时最大节汽量达到七吨左右。
3.4停用部分介质冷却器
这一点简单来说,就是停用的介质冷却器,把它的凝结水密封回收,能够有效的节约蒸汽。停用了预反应器冷却器以后,不仅可以节约循环水量,还可以避免反应热的浪费。优化了生产蒸汽运行压力后,不但能够保证运行效率,还可以回收多余的蒸汽,达到节能降耗的目标。
4MTBE装置的发展前景
在中国,MTBE仍然有一个广阔的发展空间,因为我国已经为它的发展搭建起了一个具有世界先进水平的技术平台。综合来看,在未来,MTBE的发展将会是一个以化工为主导医用更上一层楼的局面。化工用途近年来虽然已经得到了较快发展,但是还没有达到市场饱和状态,分析来看,在未来,还会有一次大规模的化工消费浪潮。目前在医药上的应用规模不全面,在未来,可能会有所增加,维持微量稳定的发展状态,但总体而言,对大局影响微乎甚微。
5结语
在化工业发展尤其迅速地今天,MTBE装置作为一种具有很大发展前景的行业,备受瞩目。化学工业作为重工业产业,稍有不慎就会对环境产生巨大的污染影响。加之化学原料的稀有,我们就更应该注重化工产业的操作安全以及节能降耗问题。MTBE的生产应用在国民经济中有着重要作用,广阔的发展前景给它的未来赋予了无限的可能。虽然目前来说,受到甲醇的供给影响,发展速度相对缓慢,但在未来,一定会开拓一片新天地。
参考文献:
[1]何德永,白应峰,王建明.齐鲁MTBE/1-丁烯装置节能优化措施[J].齐鲁石油化工,,(02):107-110+120.
[2]刘煦泽,吴明.MTBE装置单反应器运行探讨[J].当代化工,,(03):405-407.
[3]梁搏云.MTBE裂解制异丁烯装置换热网络节能研究[J].山东化工,,(04):57-60.
[4]刘春胜.MTBE合成及裂解装置节能对策的探讨[J].石油炼制与化工,,(02):83-87.
[5].MTBE装置节能分析[J].宁波节能,,(04):30-35.
篇5:常减压装置节能降耗的举措论文
常减压装置节能降耗的举措论文
摘要:利用先进的工艺和设备降低化工装置能耗,已经成为当前节能降耗的趋势。提升加热炉热效率、运用“夹点技术”优化换热网络、采用新型高效强化蒸馏的填料能够取得较理想的效果。
关键词:节能降耗;新工艺;过滤法脱盐;夹点技术
常减压装置是炼油最大的耗能装置之一,加工能耗占炼油厂总能耗的25%~30%,因此降低常减压蒸馏装置的能耗对炼油厂的节能降耗和经济指标都具有极其重要的意义。国内常减压装置最低能耗约为410.3MJ/t,而平均能耗则为518.3MJ/t。玉门油田炼化总厂装置加工能耗451.76MJ/t即10.79kg标油/t,在节能方面还是有挖掘潜力,从而节约加工成本,增加经济效益。从装置本身所需的风、电、水、蒸汽、燃料气(燃料油),可知常减压蒸馏装置降低能耗无疑应该针对以上所述改进工艺、设备,从而降低加工能耗。
1采用新技术改进工艺过程
电脱盐是原油进装置后第一道处理工序,对装置的平稳运行、设备防腐、节能降耗并改善产品质量都有至关重要的影响,并直接关系炼厂的整个生产成本,影响经济效益。针对装置超声波破乳电脱盐设备,其适宜的'操作温度为110~130℃。冬季气温较低,脱前换热设备相应散热量加大,导致原油进灌温度达不到适宜的操作温度,脱盐脱水效果不达标,影响后续操作,并加速常压塔顶低温腐蚀,进而对塔顶空冷器管管束造成应力腐蚀,对设备长周期安全平稳运行造成隐患。用过滤法〔1〕对原油拖延脱水的技术是一种对乳化原油破乳的新技术。该技术的前提是性能良好的吸附剂作为过滤材料,并制成破乳过滤桩。武汉石油化工设备研究所研制成功这种过滤材料,主要性能指标如下:颗粒直径1~4nm,平均有效半径11nm,孔容积率1.9*106m3/kg,比表面积0.68m2/g。该材料亲水性强,有一定的亲油性,强度高,在100oC以上的油品环境中不溶解,反冲洗时受到颗粒间的摩擦有非常好的抗磨损性能。经试验,结果显示利用过滤法脱盐技术,相比电脱盐,在脱后含盐量、脱后含水量、注水量、能耗和操作温度等指标上都有大幅度改进。尤其是拖延温度的大幅降低,对于北方寒冷的冬季来说,脱前换热负荷大幅度降低,能够确保原油进灌温度达到操作要求;而电耗仅为电脱盐的50%,对于降低加工总能耗的作用也非常明显。
2提高能量利用水平
2.1提高加热炉热效率
加热炉是炼化装置中给物料加热升温的最重要设备。加热炉的平稳正常运行,直接关系到进塔物料的温度。对于常压塔,进料的过汽化率(要求2%~4%)几层塔板热量传递,最终影响最下面一个侧线的质量。加热炉的正常运行,首先要确保油或燃料气的稳定供应,精确调节流量和压力。其次精心操作,加强切液,适度调节“三门一板”,确保炉膛内燃料正常燃烧。最后,要提高加热炉热效率。针对加热炉热效率,烟气余热的回收利用至关重要。目前装置的烟气余热回收系统主要是利用热管对进炉冷空气预热。这种气―气换热传热系数小,传热负荷也相对偏低,但由于露点腐蚀的限制。排烟温度不宜过低。并定期吹灰,减小热阻,也是强化对流室传热效果的有效途径。在排烟温度控制在200~500℃范围,过剩空气系数降低0.1,热效率可提升0.8%~0.9%,可见降低过剩空气系数是提高加热炉热效率的有效途径。其次,炉体散热量可以达到燃料总发热量的3%左右,加强炉体的隔热保温就显得尤为重要。
2.2优化换热网络,强化冷换设备换热效果
所谓“夹点”,即换热网络中存在的一个最先的允许的传热温差ΔTmin。利用“夹点”技术[2],对换热网络进行改进,并采取强化传热等措施,增加换热效果,可使换热效果进一步优化,提高热量利用水平。利用此技术,吉林炼油厂对第I常减压原有换热网络进行改造,使初底油换热终温由272℃提高到308℃,年节省燃料7800t,同时也降低了常压加热炉的热负荷,在条件允许的情况下,也可以加大处理量。我厂大检修中采用窄点技术对换热网络进行优化,增加了热水换热器2台和冷却器数台。结果显而易见,使原油换热终温从检修之前的(240~250)℃提高到304℃(优化设计换热终温314℃),从而降低了加热炉热负荷,提高了加工量,并确保了加热炉长周期安全平稳运行。
3采用新型、高效、低耗设备提高分分精度,以强化蒸馏
原油蒸馏的分馏精度用相邻馏分馏程的脱空和重迭来定义。馏分间馏程脱空或重迭较少,则说明分馏精度高,则分馏充分;相反地,重迭较多,没有达到预期目标,不能充分分馏。玉门油田装置常压塔采用板式塔。某炼油厂常压塔中部采用波纹填料代替,包括液体分布器,之承栅等内件,并用常三线供二中回流返回到填料上方,改造后成功投产,强化了分流能力,使分馏精度相应提高,常二线和常三线重迭也有所减少。改造投产后,常二中的变化对产品质量无影响,常三线馏程变窄。在20大检修中减压塔更换耐高温、防结焦的填料,相比来说,减底渣油的结焦得到有效缓解,开厂以来,装置运行平稳。
4结束语
目前国内常减压装置加工能耗与国际先进水平还有很大差距,节能降耗空间很大,应用夹点技术优化换热网络,结合新设备新技术强化油品换热,提高换热终温,采用新型保温隔热材料,减少炉体散热量,使用高效燃烧器以提高加热炉热效率,降低加工能耗,切实提高企业经济效益。
参考文献
[1]杜荣熙.过滤法原油脱盐脱水技术研究[J].石油炼制与化工,
[2]孟继安,牛继舜,王立安.夹点技术基本原理与应用[J].黑龙江石油化工,(2):1-4.
篇6:催化裂化工艺化学工程论文
催化裂化工艺化学工程论文
1.引言
催化裂化具体的工艺过程是为实现特定的操作条件服务的。在一定程度上也限定了操作条件的调整范围。但就反再系统来说,操作条件就包括诸多方面,如温度、剂油比、停留时间、催化剂的预提升与预提升介质、油气与催化剂的接触、两者的混合与流动、两者的分离、反应的终止、催化剂中油气的汽提、催化剂的性能以及催化剂的再生条件等。尽管操作参数众多,但平时可调整的却屈指可数,有些参数,反再系统工艺路线已经确定,也就基本确定下来,不能再调整或无法调整了。
2.操作条件的影响
催化裂化在接近常压的低压下操作,在这个压力范围内压力对热力学的影响微乎其微。较低的烃分压有利于裂化,不利于生焦,因而是有利的。最小总压取决于后续分离系统,目前在300l(Pa以下。烃分压可以通过喷入水蒸汽的方法来降低(一般喷入水蒸汽的量占进料的1~5%),也可以将一部分轻烃气体打循环,但循环量需要根据具体的经济性来确定。
3.焦炭燃烧动力学
催化裂化焦炭的收率一般在4~8%之间。在再生器的典型温度条件下,富氢化合物要么挥发,要么裂化成可挥发性组分和焦炭。催化剂再生所需要的时间主要由焦炭的较慢的燃烧速率决定。焦炭燃烧的活化能约为147kJ/mol。催化剂焦炭含量为1%、燃烧后烟气中的氧含量为1%催化剂焦炭含量为1%、燃烧后烟气中的氧含量为1%,烧焦时间与温度之阃的函数关系如图1所示。该函数关系非常重要,因为它确定了催化剡的总量与再生器的大小。减小再生器的大小与催化剂的总量很重要,原因有两个:FCC再生器在整个装置的造价中占有很大的比重,减小其大小有利于降低装置的投资;减少催化剂总量,不仅有利于减少操作费用,而且还有利于根据原料与产品的变化迅速改变催化剂。FCC装置是一个“热平衡体系”,热催化剂为裂化反应提供了部分热量。FCC装置的热平衡与催化剂的活性、原料性质、原料的预热和反应温度有关。此外,热平衡还与再生烟气CO2/CO的理想比例有关。
焦炭燃烧的一次产物有CO、CO2和H2O,CO与CO2之比是温度的函数。CO与O2反应生成CO2是自由基反应,在有固体存在的条件下反应速率会减慢。如果烟气中含有过量的空气,则只要一没有固体就会燃烧。到目前为止一直是这样。为了促进CO的燃烧,现在都加含有Pt等贵金属的`助燃剂。使CO转化成CO2也可以通过提高反应温度来实现。CO均相燃烧生成C02的活化能较高,约为293kJ/mol,在空气充足的情况下,在7000C以上CO可以完全转化。从热平衡的角度,达到7000C以上的再生温度毫无问题,但是再生器的材质和催化剂限定了最大再生温度。催化剂在高温条件下容易烧结,也易于水热失活。当然,如今的催化剂可以保证在高达850℃的高温条件下不会造成烧结破坏,但水蒸汽的老化作用要求温度要比该温度低得多。设计者在迸行反应器设计时,在降低再生温度以减小水热失活与提高再生温度以减小再生器大小之间权衡。另外一个减小催化剂水热失活的方法是采用两段再生:在第一段,在较低的再生温度条件下,进行富氢焦炭的再生;二段在较高的温度下操作。燃烧所需的停留时间是根据等温反应计算得到的,而FCC再生器并不总是等温的,尤其是催化剂颗粒温度不均匀。
再生过程中质量传递的影响要降低到最小,以便催化剂颗粒内部温度不超过气相温度。燃烧过程中的扩散控制是反应速率快造成的。扩散速率是催化剂颗粒直径的平方的函数,而反应速率则是温度的函数。颗粒直径需要在200岫1以下,再生器才能在6500c以上操作而避免颗粒内部产生高的温度梯度。固定床反应器的最小颗粒为1mm,移动床反应器的约为3mm,只有流化床反应器的催化剂颗粒直径小于200μm。对于焦炭收率很低的情况,可以考虑采取稀释空气、由此降低绝热温升的方法保护催化剂。这种方法理论上可行,实际操作过程中空气量太大,有一定的问题。
4.结语
本文介绍反应的压力、温度、停留时间和催化剂的再生等的影响,对于进一步了解催化裂化工艺相关设计问题具有一定帮助。
篇7:节能降耗是煤炭企业提高经济效益的有效途径
节能降耗是煤炭企业提高经济效益的有效途径
据有关部门统计,煤炭行业中,仅国有重点煤炭企业的主通风机、水泵就有1万余台,总装机容量200多万kW,加上其它的`风机、水泵耗电量一般都占原煤电耗的40%以上,约60亿kW・h.而这些风机、水泵,有相当一部分是六七十年代的老旧杂设备,安全运行已很难保证,就更谈不上效率了.
作 者:孙成群 作者单位:鹤壁矿务局 刊 名:煤炭经济研究 PKU英文刊名:COAL ECONOMIC RESEARCH 年,卷(期): “”(3) 分类号:F4 关键词:篇8:电机节能降耗方面论文
引言
近几年,火电机组年利用小时数逐年减少,发电机停机备用时间逐渐增加。在机组长周期停机备用时,采取合理的运行方式,在保证机组正常备用的情况下,尽可能降低备用保养的费用,是必须要考虑的问题,同时也具备可观的经济效益。
1、设备概况
湖南华电长沙发电有限公司(以下简称长沙电厂)2×600MW火电机组是湖南电网的主力机组,是国内首批、中国华电集团公司首座燃煤脱硫脱硝发电机组。发电机为东方电机股份有限公司生产的QFSN-600-2-22C型三相同步汽轮发电机,额定容量为667MVA,额定功率为600MW,额定功率因数为0.9(滞后),最大连续输出功率为655.2MW,级对数为1,定子额定电压为22kV。
发电机采用自并励静止励磁系统,采用水氢氢冷却方式:定子线圈(包括定子引线)水内冷,转子线圈氢冷,定子铁芯氢冷,定子出线氢冷。每台机组设2台定子冷却水泵电机,为YB225M-2型三相鼠笼式异步电动机,电机功率为45kW,额定电压为380V,额定电流为83.9A。2台交流密封油泵电机为YB132N型异步电机,电机功率为7.5kW,额定电压为380V,额定电流为15.4A。
1台直流事故密封油泵,功率为5.5kW。2套氢气除湿装置为北京蓝艾迪电力技术有限公司生产的电子冷凝式氢气干燥机,额定功率为50kW。冷却水取自机组闭式水系统,闭式冷却水泵电机为Y315S-4型异步电机,功率为110kW,额定电压为380V,额定电流为200.8A。
2、600MW机组停机备用期间主要能耗
长沙电厂#1机组接入220kV电网,接带长沙市区负荷,长期并网运行,#2机组接入500kV电网。由于湖南省电力紧张形势趋缓,近几年#2机组并网运行时间较短,长期停机备用。停机备用期间,发电机充氢备用,保持氢压0.300MPa,定冷水系统连续运行,保持水压0.280MPa(定冷水入口)。为保证氢气干燥,投入氢气干燥器及氢气循环风机,投入闭式水系统和密封油系统连续运行,维持运行油压0.850MPa。停机备用期间运行设备及其功率见表1[1]。如连续停机备用1个月,消耗的电能=262.5×24×30=189000(kWh),按上网电价0.47元/(kWh)计算,共计88830元。
3、降耗措施
发电机停机备用期间的能耗主要是辅机的电耗,降低耗电量,是降低能耗的'关键和出发点,因此,主要的节能措施就是在保证发电机可靠备用的前提下,通过优化辅机运行方式来降低能耗。发电机停机后,为保证机组安全可靠备用,一般采用保持额定参数的运行方式。这种方式存在充足的冗余量,在保证安全的前提下实现运行方式的优化,既可节约大量厂用电,又可延长设备检修周期,从而节省设备维护费用。
3.1氢气系统运行方式优化长沙电厂氢气系统运行额定压力为0.414MPa,停机备用时降至0.300MPa运行。考虑到发电机停机备用时没有发热源,不需要进行及时冷却,可以降低氢压运行。机组停运后,将氢压降至0.150MPa,完全可以满足发电机冷却、干燥的需求,同时为优化其他辅助系统运行方式提供了可能性。
3.2定子冷却水系统运行方式优化氢压降至0.150MPa后,此时停运定子冷却水系统,定子线圈内外压差最高只有0.150MPa,小于0.200MPa,氢气不会从线圈的接口处漏入定冷水系统,也符合电力行业规定。基于这种考虑,11月#2发电机停机备用期间,长沙电厂调整氢压至0.150MPa,停运定冷水系统。
3.3发电机密封油系统运行方式优化氢压降至0.150MPa后,发电机密封油系统压力不需要维持在0.850MPa,考虑倒换发电机密封油系统由主机润滑油系统接带,可维持密封油压在0.240MPa,保持油氢差压为0.075MPa,这种运行方式完全能够满足发电机的密封要求。月,#2发电机停机备用期间,长沙电厂调整氢压至0.150MPa后,将发电机密封油系统切换至主机润滑油带,停运发电机密封油泵。调整后系统各参数为:主机润滑油压,0.260MPa;发电机密封油压,0.250MPa;氢压,0.150MPa;油氢差压,0.050MPa。
3.4发电机干燥器及闭式水泵运行方式优化氢压降至0.150MPa后,氢气露点提高至-12.2℃(常压下氢气露点为-22.0℃)。#2发电机停机备用期间,在保证发电机内氢气足够干燥的前提下,停运氢气干燥器,保持氢气循环风机运行。氢气纯度及露点检查结果见表2。QFSN-600-2-22C三相同步汽轮发电机氢气露点要求低于-2.5℃、高于-15℃,降压备用期间,停用氢气干燥器后仍可满足要求,可以保证发电机可靠备用。停运氢气干燥器后,闭式水无实际用户,停运闭式水泵[2]。
3.5注意事项
(1)定冷水系统停用后,将发电机定子线圈内存水排尽,防止长期积水导致定子线棒结垢。
(2)发电机停机备用期间,每天检测#2发电机内氢气纯度及露点,防止发电机内部结露。
(3)发电机氢气纯度降低时,及时进行补排氢置换,保证氢气纯度在95%以上。
4、降耗效果
按照长沙电厂#2发电机年运行2752h、停机备用6008h计算,每年可节约电量262.5×6008=1577100(kWh),节约电费约74万元/年,节约设备维护费用约6万元/年,共计80万元/年,达到了预期的节能效果。
5、结束语
纵观整个工作的全局,有两点需强调:一是节能降耗必须以机组安全可靠备用为前提,不能为片面追求降低能耗而对机组安全产生影响;二是节能降耗工作忌讳“眼高手低”,必须坚持从小处着手,以取得更大收益。电力行业的节能降耗工作对解决我国能源问题至关重要,也是实现我国“十一五”节能降耗目标的根本保证,节能降耗工作已列入各个发电企业的重点工作项目。
降低厂用电设备的电能消耗是发电企业直接增加产出提高能源转化效率的有效途径,应通过借鉴经验和自主创新改革,坚持不懈地把节能降耗工作抓好、做好。
参考文献:
[1]湖南华电长沙发电有限公司600MW集控主机规程:Q/CSFD10301102―2015[S].
[2]电力设备预防性试验规程:DL/T596―[S].
篇9:配电网节能降耗论文
【摘要】
文章分析了配电网络降低有功损耗的各种技术措施和管理手段。结合东莞城市经济发展与城市建设的现状,总结了当前配网进行节能改造所面临的一些客观困难,由此提出了一些相关建议。
【关键词】
篇10:配电网节能降耗论文
我国“十一五”规划明确提出了节能减排的任务和目标,电网公司做为电能等资源综合配置、运营和管理的主要企业,既承担服务社会,保证安全、可靠、优质供电的责任,又是执行国家节能政策任务的关键部门。电力系统本身是一个能耗大户,而城市配电网更是电力系统能量损耗的主体部分,实现配电网的节能降耗对供电企业提高经济效益,实现目标利润起着举足轻重的作用。由于负荷增长速度快而配电网建设投资滞后,配电网在节能降耗方面有着很大的挖掘潜力。通过配网节能降耗工程惠及千家万户,优质服务于社会也是供电局期望和追求的目标。
一、降低损耗的技术措施
1.合理调整运行电压。通过调整变压器分接头、在母线上投切电力电容器等手段,在保证电压质量的基础上适度地调整运行电压。因为有功损耗与电压的平方成正比关系,所以合理调整运行电压可以达到降损节电效果。
2.合理使用变压器。配电变压器的损耗是配电网损耗的主要组成部分。因此,降低配电变压器的损耗对于降低整个配电网的损耗效果非常明显。方法主要有:使用低损耗的新型变压器、合理配置配电变压器容量等。
3.平衡三相负荷。如果三相负荷不平衡,会增加线路、配电变压器的损耗。
4.合理装设无功补偿设备,优化电网无功分配,提高功率因数。
5.合理选择导线截面。线路的能量损耗同电阻成正比,增大导线截面可以减少能量损耗。
6.加强线路维护,防止泄漏电。主要是定期巡查线路,及时发现、处理线路泄漏和接头过热事故,可以减少因接头电阻过大而引起的损失,及时更换不合格的绝缘子,对电力线路沿线的树木经常修剪树枝,还应定期清扫变压器、断路器及绝缘瓷件等。
7.合理安排检修,提高检修质量。电力网按正常运行方式运行时,一般是既安全又经济,当设备检修时,正常运行方式遭到破坏,使线损增加。因此,设备检修要做到有计划,要提高检修质量,减少临时检修,缩短检修时间,推广带电检修。
8.推广应用新技术、新设备、新材料、新工艺,降低电能损耗。
9.调整负荷曲线,避免大容量设备在负荷高峰用电,移峰填谷, 提高日负荷率。
二、降低损耗的管理手段
1.加强计量管理,做好抄、核、收工作。
2.实行线损目标管理。供电公司对下属管理部门实行线损目标管理责任制,签订责任书,开展分所、分压、分线考核,并纳入内部经济责任制,从而调动职工的工作积极性。
3.定期召开用电形势、线损分析会,开展线损理论计算。
4.定期对馈线电流平衡情况、三相负荷不平衡情况进行检查和调整。
三、当前城市配电网节能改造的难点
1.负荷密度大,发展速度过快。
以东莞长安镇为例。长安面积为83.4km2,最大负荷达到93.8万KW,从节能降耗的角度来看,这种大密度用电负荷需要更多的变电站布点、更多的出线间隔、更多的线路(电缆)走廊。但受土地资源约束和城镇规划的局限,目前要进一步增加变电站布点、出线间隔和走廊难度极大。这在一定程度上也与负荷超常规发展以至超出城市规划的承受极限有重要的关系。如何解决配电网的空间需求是目前最为头痛的难题。
2.居民用户对电力设施的抵触情绪。
电力设施的电磁辐射是一个众说纷纭的问题,目前尚无明确结论,但是广大居民用户因三人成虎的从众心理,对电磁辐射问题存在强烈的恐惧感;加之配电设备的噪音污染、高电压等原因,居民用户更是对配电设备的布点安装持莫大的抵触情绪。致使东莞东城市及其乡镇中普遍存在“只要电力不要设备”的现象,供电企业的配网改造和发展阻力极大。 3.节能变压器生产成本高企。配电变压器的有功损耗是配电网损耗的重要组成部分。目前国内已经开发出各种节能型的变压器,主要是显着降低了变压器的空载损耗,但因其造价比传统配电变压器高出30%~80%,而将健康的高能耗配变更换为节能变压器的经济回收期一般达到左右。因此,出于经济成本的考虑,无论是专变用户还是供电企业,要放弃现在尚能运行的S7、S9系列改用S11、S13等系列的配变的主观愿望基本上是没有的。这在很大程度上影响了配电变节能降耗改造工作的进度。
4.配变无功补偿最佳容量的`确定。
配变低压无功动态补偿是降低配网有功损耗的有效措施,目前东莞100KVA及以上的公用变压器均要求进行动态投切无功补偿。然而无功补偿的分组容量和总容量的确定是一个相对复杂的优化问题,与配变容量、负荷曲线、功率因数等因素密切相关,并涉及到电压水平问题。目前对所有配变均按30%容量左右来配置补偿容量不尽合理,造成部分补偿度不足、部分补偿容量过剩浪费的情况,且电压合格率还有提升空间,另外,无功补偿如何分组未能结合各配变负荷的实际,造成无功补偿效率较低、降损效果远达不到理论估算值。
5.电力设施被盗现象猖獗。
目前东莞电力设施偷盗现象相当猖獗,技术手段也越来越高。从380V到220KV的各电压等级的设备都是被盗对象。以380V低压线路为例,只要拉一条较大截面的电缆,短期内就会被盗。由于我局人手紧缺、工程量大,迫于压力,只好采用截面较小的电缆来降低被盗的风险,这显然是既不利于节能,又不足于满足负荷的需求,实在是无奈之举。
四、对策和思考
1.加强与政府的沟通和对群众的宣传。通过与政府和群众的沟通,争取得到市政规划和广大群众的密切配合,让百姓减少对电力设施的顾虑,增进对电力建设的理解和接受,确保电力建设与配网的顺利进行。
2.与变压器生产企业联手向政府争取政策扶持。通过政府税收、财政补偿、节能奖励等政策的落实,促进节能变压器厂家生产成本的下降,推动节能变压器的广泛应用。
3.加强对配网无功补偿的研究。通过和科研院的合作,开展配网无功补偿的研究,确定配网无功补偿的优化方案与技术细节,以更少的无功补偿资金获得更大的节能效益。
4.与公安部门等联手,加强防盗工作。通过与公安部门的密切合作,加强防盗巡查和对盗贼的打击力度。此外,应着手开展反窃电活动,偷电行为越来越巧妙,并向技术型发展。对用户应装设防窃电的电能表、电量监视器等。另外,加大打击偷电的力度,不定时到计量点现场察看,维护供电企业电力市场的正常运营。
五、结语
目前城市配电网节能改造面临不少难点,因此,需根据不同配网实际情况,选择适合本地配网降损的综合方案,以取得更高的社会效益和经济效益。
篇11:节能降耗的论文
炼油化工企业节能降耗技术分析
摘要:炼油化工行业是高耗能、高污染的行业,保证炼油化工企业的可持续发展,需要降低化工生产过程中的能源消耗,提高能源利用率。基于此,本文对炼油化工企业的节能状况进行了介绍,并分别从减少动力能耗的技术、改善工艺条件的具体方法以及催化剂与阻垢剂的应用等方面,分析了炼油化工企业的节能降耗技术,从而提高炼油化工企业的经济效益。
篇12:节能降耗的论文
近几年,我国的炼油化工行业得到了飞速发展,企业的规模和实力不断扩大,但与此同时,由于我国大型炼油化工厂设备密度比较大,且对能源的利用效率远低于发达国家,因而能源的浪费现象十分严重。
1、炼油化工企业节能状况概述
近年来,我国炼油企业不断探索提高能源利用率的方法,虽然降低了部分乙烯装置的能耗和物耗,但与发达国家的先进水平相比,还是相差甚远,而且,不同能源在炼油化工企业中的消耗水平也不尽相同。在我国,年产量达到千万吨规模的炼油化工企业屈指可数,从整体上来看,我国的炼油企业装置规模偏小,存在许多小型炼油厂。若要降低我国炼油企业的对能源的消耗,首先要扩大炼油厂内的装置规模,可以新建大规模的炼油厂,也可以扩建原有的炼油厂,增加炼油厂的年产量,除此之外,还可以把小型炼油厂合并,另那些达不到标准的炼油厂停止工作。其次,还应不断引进国外的先进科学技术,为炼油化工企业配置有利于节能减排的设备装置,加大对于节能减排的资金投入,并及时攻克技术上面的难题,改善炼油化工企业的工艺条件,充分利用资源,促进我国炼油化工企业的不断发展。近几年,延安炼油厂不断革新技术,创新炼油厂的管理方法,使延安炼油厂常压装置的加工能力达到800万吨/年,催化装置的加工能力高达400万吨/年,推动了延安炼油厂的规模化、一体化发展[1]。
2、炼油化工企业中节能降耗技术分析
2.1炼油化工企业减少动力能耗的技术
大多炼油化工企业通常采用变频节能调速的方法减少对动力能的消耗,该方法可以改善传统的静态阀门程序,保证电机拖动系统可以在长时间的工作中保持动态平衡,不仅如此,变频节能调速方法还可以解决因为电机长时间工作,造成电能浪费等问题。还有一种减少动力能消耗的技术,即优化炼油化工企业的供热系统。在化工生产过程中,不可避免会生成大量污水,在浪费水资源的同时,也消耗了大量的电能以及热能,将这些污水进行回收利用,可以实现对水资源的二次利用。延安炼油厂通过引用先进的污水处理技术,提高了对水资源的利用率,真正做到了节能减排,为企业节约了能源。
2.2炼油化工企业改善工艺条件的措施
改善炼油化工企业的工艺条件,需要降低化工生产反应的外部压力。化工生产中的主要能耗是化学反应中所消耗的能量,只有在了解化工生产外部压力的条件下,才能更好地控制化学反应带来的能量消耗,通过降低反应物在传递过程中的能量,使生产总能减小。在掌握反应物在化工生产过程中的反应条件的基础上,可以控制反应物在生产过程中的吸热程度,从而降低化工生产过程中的温度,提高热能的利用率。了解化学反应中的副反应,并提高对热能的利用率,可以降低化工生产中的能量消耗。
2.3炼油化工企业对新技术、新设备以及新工艺的引进
新科技不仅可以保证将能源消耗降到最低,同时也能够使企业的利益最大化。延安炼油厂在化工生产中,引进了结晶分离技术,该技术能更好地适应化学反应,提高炼油厂的能源利用率。提高炼油化工企业的能源利用率,也可以引进国外知名的新型设备,如:加热炉、换热器、分馏塔等设备。化工生产的基础是分离和提纯,同时分离和提纯是化工生产中浪费最为严重的`两个环节,所以,引进科技含量高的设备,有利于减少能源在提纯和分离环节的浪费,但是一定要注意,引进先进设备时,应分析设备的可操作性、节能性以及对能源的转换效率,促进化工生产的节能降耗。
2.4炼油化工企业对阻垢剂及催化剂的应用
第一,炼油化工企业对阻垢剂的应用。大部分机电设备在长时间使用之后,都会产生大量的污垢,污垢的存在会使设备的性能受到影响,降低设备的工作效率,同时也浪费了大量的化工能源。去除机电设备中的污垢,可以利用阻垢剂定期清洗设备,达到维护设备正常运转的目的,减少化工生产中的能源浪费。
第二,炼油化工企业对催化剂的使用。催化剂可以用来增强化工生产中的化学反应转换率,化工生产中常用的催化剂有两种,分别是:加快化学反应的催化剂以及减缓化学反应的催化剂,虽然这两种催化剂的作用不同,但是它们都可以降低对能源的消耗。延安炼油厂依据科学合理的办法,将催化剂应用到化工生产过程中,在减少化工生产过程中副产物的同时,提高了对原材料的利用率,真正实现了节能降耗的目标[2]。
2.5炼油化工企业蒸馏中对热泵技术的应用
在化工生产过程中,蒸馏是应用最广泛的节能降耗方法,延安炼油厂在蒸馏过程中应用热泵技术,将蒸馏塔顶部低温位的热量传递到蒸馏塔底部的高温位,降低了蒸馏过程中的能量消耗。目前,市场上有间接热泵蒸馏和直接热泵蒸馏这两种蒸馏系统,化工企业可以按照自己的需要选择蒸馏系统,实现化工企业的节能降耗目标。
3、总结
综上所述,炼油化工企业使用合理的工艺并加强各装置之间的能量转化效率,可有效减少能源消耗,提高能源利用率。通过使用上述炼油化工企业中节能降耗技术,可以提高对资源的利用率、维护设备正常运转、增强能源的转换效率,真正意义上实现节能降耗的目标。因此,炼油化工企业在化工生产过程中,应实施节能降耗技术,减少环境污染以及资源浪费现象的发生,提高企业经济效益。
参考文献:
[1]代超奇.炼油化工企业节能降耗技术思考[J].化工管理,,26:302.
[2]张小明,张艾秋,王嬴.常减压蒸馏装置节能降耗技术改造措施研究[J].当代化工研究,,05:136-137.
篇13:燕山石化乙烯装置节能降耗措施及成效
燕山石化乙烯装置节能降耗措施及成效
燕山石化乙烯装置生产能力为71×104t/a,2005年装置能耗为684.9kg标油/t乙烯.近年来,为降低装置能耗,采取如下措施:①优化原料结构,提高乙烯收率,石脑油中对乙烯收率影响最大的链烷烃含量由2006年的69%提高到2009年的71%,裂解性能得到改善,加氢尾油(HVGO)中的芳烃指数(BMCI)由2007年的14降低到2009年的`7;到2008年,以石脑油为代表的轻质原料的加工量已达62.8%,2009年5月乙烯收率已达32.13%.②优化蒸汽平衡,在所有裂解炉上安装空气预热器,改高压锅炉给水泵的运行方式为电泵运行、汽泵备用,降低低压蒸汽产量15t/h,解决了低压蒸汽过剩问题,消除了放空现象.③裂解炉烧焦时间由57h缩短了10h,降低了烧焦的消耗,急冷油塔釜温度平均提高10℃,减少中压蒸汽耗量15t/h.④加强设备检修和维护管理,在负荷不变的情况下,超高压蒸汽消耗平均下降了40t/h.上述措施实施后,乙烯装置2009年上半年的装置能耗为568kg标油/t乙烯,比2005年下降17.1%.
作 者:孙国臣 Sun Guochen 作者单位:中国石化北京燕山分公司,北京,102500 刊 名:中外能源 英文刊名:SINO-GLOBAL ENERGY 年,卷(期):2009 14(11) 分类号:X7 关键词:乙烯 能耗 收率 优化【催化裂化装置节能降耗的有效途径论文】相关文章:
1.节能降耗论文
6.节能降耗心得体会
7.节能降耗措施
8.节能降耗方案
9.节能降耗工作总结
10.节能降耗标语
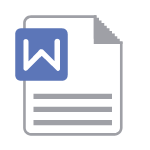





文档为doc格式